|
 |
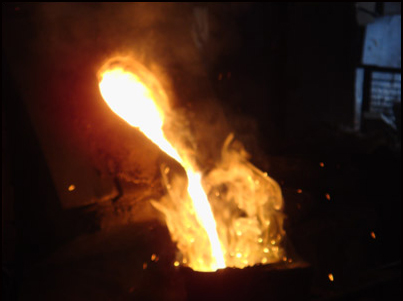 |
|
The raw material comprises of combination of Pig Iron, Mild Steel, some iron scrap material and cast iron. The correct proportions have to be chosen for different vehicles depending on properties required by their matching components and as specified by the original equipment manufacturers. |
|
This conglomerate is melted in an induction furnace supplied by the world-renowned expert fabricators M/s. ElectromechPowermelt Ltd, by heating under controlled electric supply (high ampere, low voltage) for a specified time and attaining required melting temperature of 1400-2000°c. |
|
A small quantity is tested in a sample cup, for the material composition. The required grade of Carbon, Manganese and Silicon is ensured in the first step by the in-house metal analyzer supplied by Suyash Enterprise, Pune. |
|
The other impurities such as Sulphur and Phosphorus are controlled to the permissible levels. Slag material is removed before some additives like Nickel, Molybdenum, Chromium etc. are added in small quantities as recommended to develop desired strength, hardness and surface finish in the final product. Next, the molten metal is taken into ladles and poured into rotating die machines where it is cast centrifugally. |
|
We are following step inspection method. specially designed Jigs and Fixtures are develop to act as a GO, NO-GO gauge during manufacturing stages. After rough machining, every piece is thoroughly inspected for casting defects or cracks and for sufficient material thickness, wherever further machining is to be done. |
|
Then hardness is checked for each and every piece on a Brinell hardness tester. Finally, the products are thoroughly checked and then our logo mark "MDT" & "Jai No.1" are stamped. Finally they are dipped into special anti-corrosion agents to enhance shelf life and high workability. |
|
 |
|
|